What is Porosity in Welding: Comprehending Its Causes and Enhancing Your Skills
What is Porosity in Welding: Comprehending Its Causes and Enhancing Your Skills
Blog Article
Understanding Porosity in Welding: Checking Out Causes, Impacts, and Avoidance Methods
Porosity in welding is a persistent difficulty that can significantly affect the top quality and integrity of welds. As experts in the welding industry are cognizant, recognizing the causes, effects, and prevention strategies connected to porosity is important for achieving robust and trusted welds. By delving into the origin of porosity, examining its harmful results on weld high quality, and exploring efficient prevention techniques, welders can boost their expertise and abilities to create top notch welds constantly. The complex interplay of factors adding to porosity calls for an extensive understanding and an aggressive strategy to make certain successful welding outcomes.
Typical Reasons For Porosity
Contamination, in the form of dirt, oil, or rust on the welding surface, produces gas pockets when heated, leading to porosity in the weld. Inappropriate protecting happens when the protecting gas, commonly made use of in procedures like MIG and TIG welding, is incapable to totally shield the molten weld pool from reacting with the bordering air, resulting in gas entrapment and subsequent porosity. Furthermore, insufficient gas coverage, usually due to wrong circulation rates or nozzle positioning, can leave components of the weld unprotected, enabling porosity to develop.
Effects on Weld Quality
The visibility of porosity in a weld can significantly jeopardize the general high quality and integrity of the welded joint. Porosity within a weld produces spaces or dental caries that damage the structure, making it a lot more at risk to cracking, corrosion, and mechanical failure. These gaps act as tension concentrators, minimizing the load-bearing capability of the weld and raising the chance of early failure under used stress. On top of that, porosity can also act as potential sites for hydrogen entrapment, further aggravating the destruction of the weld's mechanical properties.
Additionally, porosity can hinder the effectiveness of non-destructive testing (NDT) strategies, making it challenging to detect other problems or discontinuities within the weld. This can lead to substantial safety concerns, especially in vital applications where the architectural integrity of the welded components is paramount.

Prevention Techniques Summary
Offered the detrimental effect of porosity on weld top quality, reliable avoidance strategies are critical to preserving the structural integrity of bonded joints. Among the main prevention strategies is detailed cleansing of the base materials prior to welding. Impurities such as oil, grease, rust, and dampness can contribute to porosity, so ensuring a tidy job surface is essential. Correct storage of welding consumables in completely dry conditions is also crucial to avoid wetness absorption, which can bring about gas entrapment during welding. In addition, picking the suitable welding criteria, such as voltage, current, and take a trip speed, can aid minimize the danger of porosity development. Guaranteeing appropriate protecting gas go to the website circulation and coverage is one more critical prevention technique, as insufficient gas protection can lead to climatic contamination and porosity. Ultimately, appropriate welder training and qualification are crucial for implementing Click Here safety nets successfully and regularly. By integrating these avoidance strategies into welding techniques, the event of porosity can be dramatically lowered, leading to stronger and more dependable welded joints.
Importance of Proper Protecting
Appropriate protecting in welding plays a vital duty in protecting against climatic contamination and guaranteeing the integrity of bonded joints. Protecting gases, such as argon, helium, or a mixture of both, are generally utilized to shield the weld swimming pool from reacting with components airborne like oxygen and nitrogen. When these reactive elements enter call with the hot weld pool, they can create porosity, bring about weak welds with decreased mechanical properties.
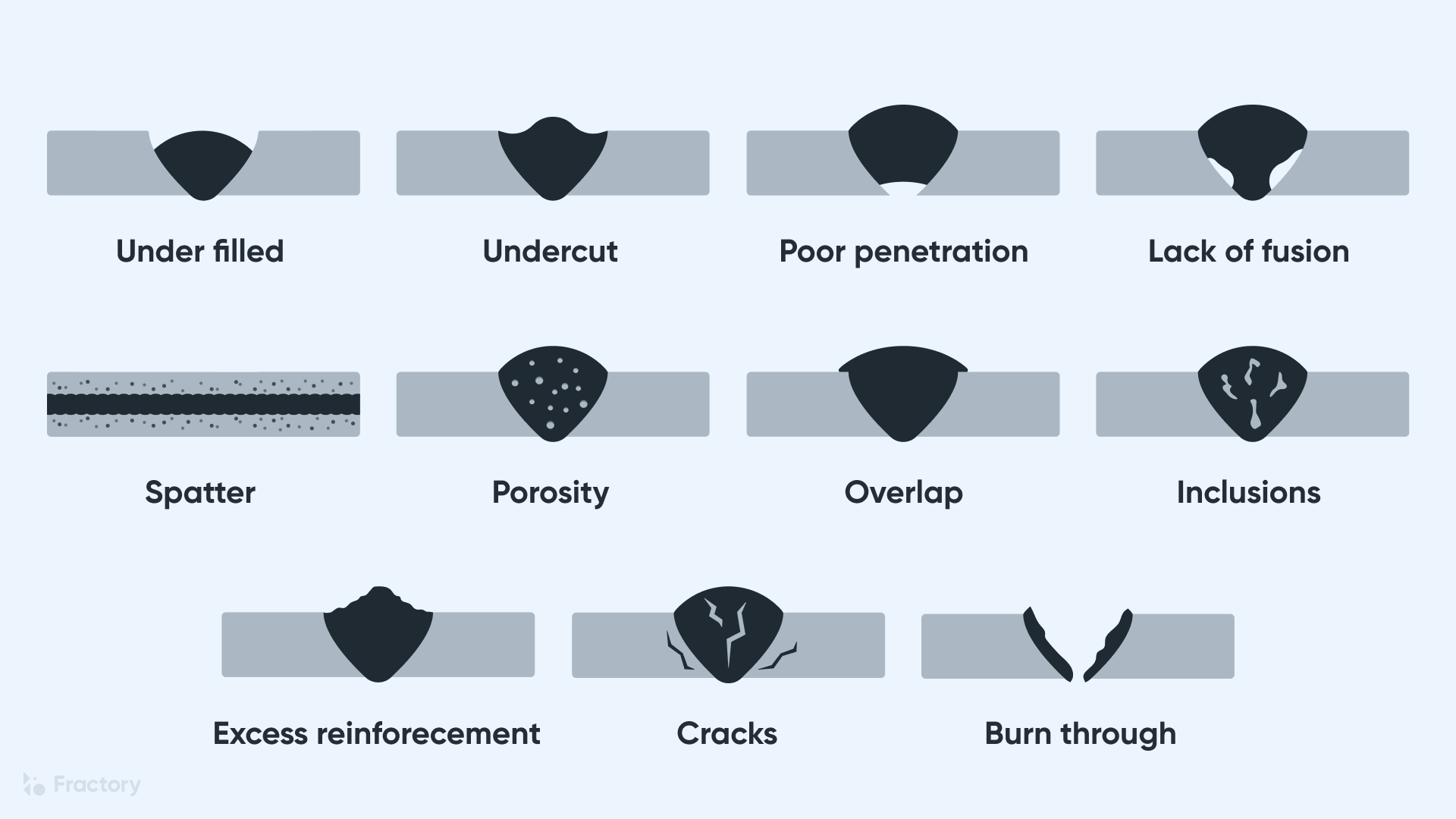
Insufficient protecting can result in different issues like porosity, spatter, and oxidation, jeopardizing the architectural honesty of the bonded joint. Adhering to appropriate shielding methods is crucial to produce top notch welds with marginal defects and make sure the longevity and dependability of the welded parts.
Surveillance and Control Methods
Exactly how can welders efficiently keep track of and manage the welding process to ensure optimal outcomes and protect against flaws like porosity? By continually keeping an eye on these variables, welders can determine variances from the optimal problems and make prompt adjustments to protect against porosity formation.

Furthermore, executing appropriate training programs for welders is essential for keeping an eye on and managing the welding process successfully. What is Porosity. Informing welders on the significance of preserving consistent parameters, such as correct gas shielding and travel rate, can assist avoid porosity concerns. Routine assessments and qualifications can likewise ensure that welders excel in surveillance and managing welding processes
Moreover, the use of automated welding systems can boost monitoring and control abilities. These systems can precisely manage welding parameters, minimizing the possibility of human mistake and guaranteeing regular weld quality. By integrating advanced tracking modern technologies, training programs, and automated systems, welders can efficiently check and manage the welding procedure to minimize porosity flaws and attain premium welds.
Verdict
Report this page